University of Missouri Makes Breakthrough in 3D Printing: Multi-Material Marvels Made Simple
Researchers at the University of Missouri have developed a revolutionary new method for 3D printing complex devices using multiple materials! This means intricate objects with features like sensors, circuits, and even textiles can all be created with a single machine.
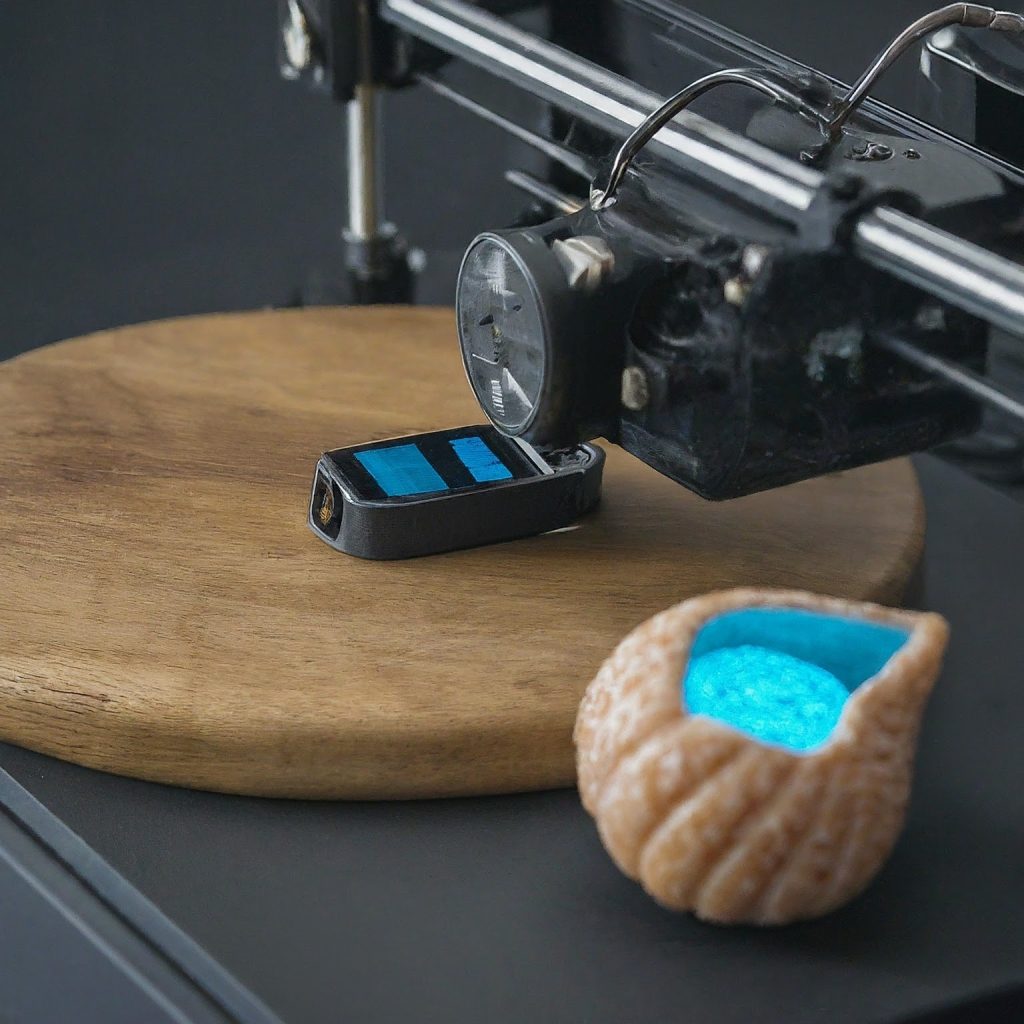
This innovative technique, called the Freeform Multi-material Assembly Process, promises to significantly impact various fields. Here’s why this is a game-changer:
- Multi-material marvels: This 3D printer can combine plastics, metals, and semiconductors into a single design.
- Farewell, Frankenstein: Traditional methods for creating complex objects involve multiple steps and machines. This new method simplifies the process significantly.
- Waste not, want not: The traditional approach often generates waste. This new technique is more environmentally friendly.
- Inspired by nature: Mimicking how organisms combine different materials for structure and function, this method allows for embedded sensors and functionalities.
How it Works
The magic behind this 3D printer lies in its special features:
- Three’s a charm: The machine has three nozzles. One prints the base structure, another uses a laser to precisely carve shapes and materials, and the last adds functional materials for specific purposes.
- Building functionalities: After creating the base and tailoring it with the laser, the printer adds additional materials to give the final product its desired functionalities.
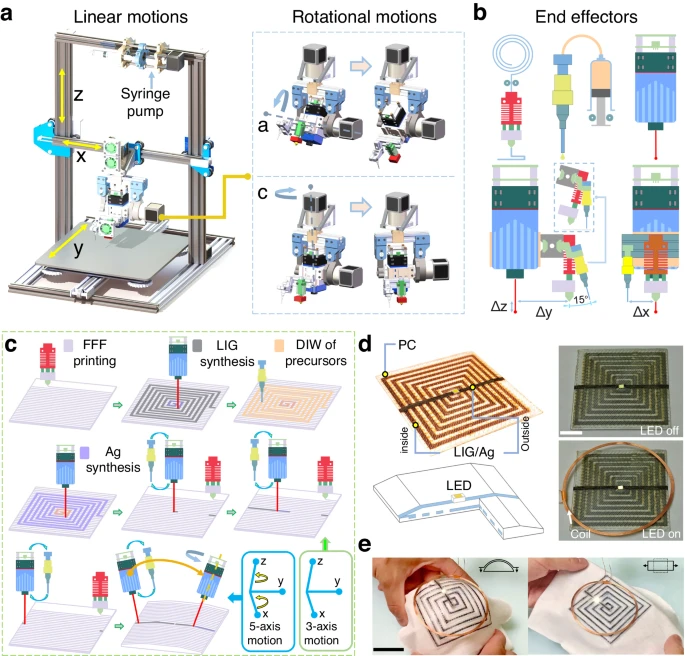
Absolutely! Here’s the information using A, B, C, and D identifiers without the “Previously titled” prefix:
A. FMAP Platform with Actuation System
This image depicts the Freeform Multi-material Assembly Process (FMAP) platform and its mechanisms for precise movement (both linear and rotational).
B. FMAP Print Heads
This image showcases the various print heads used in FMAP:
Filament extrusion (FFF)
Direct ink writing (DIW)
Functional layer integration (FLI)
It also highlights the positioning of each head for optimal printing.
C. Creating a 3D Wireless LED Circuit
This image illustrates the step-by-step process of fabricating a 3D wireless LED circuit with laser-induced graphene (LIG) electrodes and silver using FMAP. Color coding helps differentiate materials:
Light purple: 3D printed filament
Grey: LIG traces
Light orange: Silver precursor
Light blue: Finished silver electrodes
D. 3D Wireless LED
This image combines a schematic and a photograph of the completed 3D wireless LED circuit.
E. Stretchable 3D Wireless LED on Fabric
This image displays a fabricated 3D wireless LED with LIG electrodes (made from lignin) and silver, mounted on a piece of cloth. The LED is being pressed onto a curved object, demonstrating its flexibility. A scale bar of 10 millimeters is included for reference.
Benefits for Everyone
This breakthrough has exciting implications for various sectors:
- Researchers: They can create more intricate prototypes with embedded sensors, saving time and resources.
- Businesses: Faster in-house prototyping can lead to quicker product development cycles.
- Consumers: Imagine wearable health monitors or smart clothing seamlessly integrated into our daily lives!
This technology is still under development, but the possibilities are endless. Researchers are exploring commercialization opportunities, and the future of manufacturing looks bright!
Do you have any ideas for how this new 3D printing method could be used? Share your thoughts in the comments below!
Reference: https://www.nature.com/articles/s41467-024-48919-5